당신은 주제를 찾고 있습니까 “박막 증착 공정 – 원숭이가 이해하기에는 조금 어려운 증착공정, 이온주입, CVD, PECVD, ALD, AMAT, 유진테크, 원익IPS, 주성엔지니어링“? 다음 카테고리의 웹사이트 ppa.maxfit.vn 에서 귀하의 모든 질문에 답변해 드립니다: https://ppa.maxfit.vn/blog. 바로 아래에서 답을 찾을 수 있습니다. 작성자 디벨럽_DEVELOP 이(가) 작성한 기사에는 조회수 32,018회 및 좋아요 663개 개의 좋아요가 있습니다.
화학반응을 통해 웨이퍼에 곱게 화장을 하는 증착 공정(deposition) 웨이퍼 위에 원하는 분자 또는 원자 단위의 물질을 박막의 두께로 입혀 전기적인 특성을 갖게 하는 일련의 과정을 증착(Deposition)이라고 합니다.
박막 증착 공정 주제에 대한 동영상 보기
여기에서 이 주제에 대한 비디오를 시청하십시오. 주의 깊게 살펴보고 읽고 있는 내용에 대한 피드백을 제공하세요!
d여기에서 원숭이가 이해하기에는 조금 어려운 증착공정, 이온주입, CVD, PECVD, ALD, AMAT, 유진테크, 원익IPS, 주성엔지니어링 – 박막 증착 공정 주제에 대한 세부정보를 참조하세요
증착공정에 대해 공부해봤는데..
좀 어려운 부분이 많아
저도 100% 이해 한 건 아니네요…
하지만 증착공정에서 앞으로의 투자 방향을 알기에는 어렵지 않았습니다.
잘못된 부분이나 부족한 부분 있으면 댓글 남겨주세요~^^
박막 증착 공정 주제에 대한 자세한 내용은 여기를 참조하세요.
제 36화, 반도체 8대 공정 – 5.박막 증착(Deposition) 공정
반도체 8대 공정. 5번째 순서. 박막 증착 공정. (Deposition). 입니다. 우선. 박막(Thin Film)이란? 기계가공으로는 실현불가능한.
Source: blog.naver.com
Date Published: 3/3/2022
View: 1917
웨이퍼에 균일한 ‘도화지’를 입히는 사람들_Thinfilm기술담당
반도체 공정에서 ‘박막(Thinfilm) 공정’은 웨이퍼(Wafer) 표면에 분자 또는 원자 단위의 물질로 1㎛(마이크로미터) 이하의 매우 얇은 막을 입히는 …
Source: news.skhynix.co.kr
Date Published: 7/14/2022
View: 200
[World Tech] 반도체 8대 공정 ⑤박막증착 공정 – 월드투데이
물리적 증착법은 주로 금속 박막의 증착에 사용되며 화학반응이 수반되지 않는 증착법이다. 물리적 증착법에는 Thermal evaporation, E-beam evaporation, …
Source: www.iworldtoday.com
Date Published: 11/12/2021
View: 5796
[반도체 8대공정] 5. 박막 증착 공정 – 학부연구생의 공부일지
– PVD(Physical Vapor Deposition)란 열 또는 충격과 같은 물리적 반응을 통해 박막을 표면에 증착하는 방식이다. 3. Thermal Evaporation (열 증착법). 1 …
Source: cvlab.tistory.com
Date Published: 10/2/2021
View: 9860
반도체 8대공정 4탄, 박막(Thin Film)증착(Deposition)공정 개념 …
이 웨이퍼에 전기적 특성을 입히는 공정을 박막(Thin Film)증착(Deposition)공정이라고 합니다. Deposition은 크게 2가지 방식으로 분류할 수 있습니다.
Source: yeonidoggi.tistory.com
Date Published: 7/17/2022
View: 1410
반도체 공정 – 박막 공정(PVD)
박막 증착 공정은, 여러층을 쌓아 바로 아래층의 회로가 위층의 회로와 가까워지면, 서로에게 영향을 주기 때문에 불량 제품이 생산될 수 있기 때문에, …
Source: slaks1005.tistory.com
Date Published: 8/15/2021
View: 4754
주제와 관련된 이미지 박막 증착 공정
주제와 관련된 더 많은 사진을 참조하십시오 원숭이가 이해하기에는 조금 어려운 증착공정, 이온주입, CVD, PECVD, ALD, AMAT, 유진테크, 원익IPS, 주성엔지니어링. 댓글에서 더 많은 관련 이미지를 보거나 필요한 경우 더 많은 관련 기사를 볼 수 있습니다.
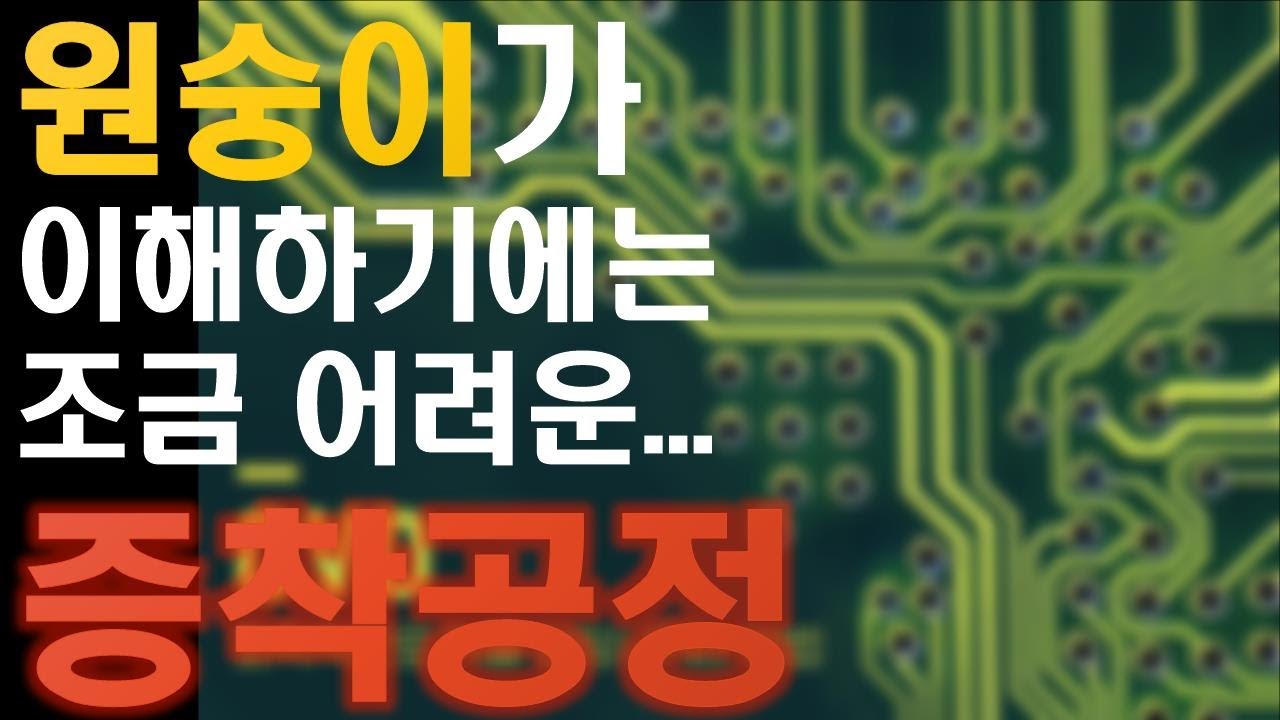
주제에 대한 기사 평가 박막 증착 공정
- Author: 디벨럽_DEVELOP
- Views: 조회수 32,018회
- Likes: 좋아요 663개
- Date Published: 2020. 6. 24.
- Video Url link: https://www.youtube.com/watch?v=fQ7qf5BpHqs
반도체 8대 공정 6탄. 반도체가 원하는 전기적 특성을 갖게 하려면? – 삼성반도체이야기
“반도체 안에 건물을 쌓아 올린다??” 무슨 말인지 궁금하시죠?
사람의 손톱보다 작고 얇은 반도체 칩을 수직으로 잘라 고배율 전자현미경을 통해 들여다 보면 상상할 수 없을 만큼 미세하고 수 많은 층(layer)이 마치 고층 빌딩처럼 높다랗고 견고하게 쌓여 있는 것을 발견하실 수 있습니다.
이러한 구조를 형성하기 위해서는 반도체의 원재료가 되는 단결정 실리콘(Si) 웨이퍼 위에 단계적으로 박막을 입히고 회로 패턴을 그려 넣은(포토공정) 다음, 불필요한 부분을 선택적으로 제거(식각공정)하고 세정하는 과정을 여러 번 반복 하게 되는데요.
이번 시간에는 식각 공정(Etching)에 이어 ‘얇은 막’을 뜻하는, ‘박막(thin film)’공정에 대해 알아보고 이후 반도체가 전기적 특성을 갖도록 만드는 과정에 대해 살펴 보도록 하겠습니다.
■ 얇아도 너~무 얇다! 눈 뜨고도 볼 수 없는 두께의 얇은 막, 박막(thin film)
흔히 사전적 의미로 ‘박막(thin film)’이란, 기계가공으로는 실현 불가능한 두께인 1마이크로미터(μm, 100만분의 1미터) 이하의 엷은 막이라고 정의되어 있습니다.
반도체 공정에서는 반도체가 원하는 전기적인 특성을 갖도록 하기 위해 분자 또는 원자 단위의 물질을 박막의 두께로 촘촘히 쌓게 됩니다. 워낙 두께가 얇기 때문에 웨이퍼 위에 균일하게 박막을 형성시키는 데에는 정교하고 세밀한 기술력이 필요합니다.
예를 들어, 8인치 크기의 웨이퍼(반경 100mm)에 두께가 1마이크로미터(μm)의 박막을 씌운다고 가정해 보겠습니다. 이는 곧 반경 100m크기의 대운동장에 모래를 1mm 이하의 두께로 균일하게 쌓는 것과 같은 수준이니 박막을 씌우는 일이 얼마나 고난이도 기술력이 필요한 작업인지 감이 오시나요?
■ 화학반응을 통해 웨이퍼에 곱게 화장을 하는 증착 공정(deposition)
웨이퍼 위에 원하는 분자 또는 원자 단위의 물질을 박막의 두께로 입혀 전기적인 특성을 갖게 하는 일련의 과정을 증착(Deposition)이라고 합니다.
증착의 방법은 크게 물리적 기상증착방법(PVD, Physical Vapor Deposition)과 화학적 기상증착방법(CVD, Chemical Vapor Deposition)으로 나뉘게 되는데요.
▲반도체 증착 구조
물리적 기상증착방법(PVD)은 금속 박막의 증착에 주로 사용되며 화학반응이 수반되지는 않습니다.
화학적 기상증착방법(CVD)은 가스의 화학 반응으로 형성된 입자들을 외부 에너지가 부여된 수증기 형태로 쏘아 증착시키는 방법으로 도체, 부도체, 반도체의 박막증착에 모두 사용될 수 있는 기술입니다.
이러한 이유로 현재 반도체 공정에서는 화학적 기상증착방법(CVD)을 주로 사용하고 있습니다. 화학적 기상증착방법(CVD)은 사용하는 외부 에너지에 따라 열 CVD, 플라즈마 CVD, 광CVD 등으로 세분화 되는데요, 특히 플라즈마 CVD의 경우, 다른 CVD에 비해 저온에서 형성이 가능하고 두께 균일도를 조절할 수 있으며 대량 처리가 가능하다는 장점 덕분에 최근에 가장 많이 이용되고 있습니다.
증착 공정을 통해 형성된 박막은 크게 회로들 간 전기적인 신호를 연결해 주는 금속막(전도)층과 내부 연결층을 전기적으로 분리하거나 오염원으로부터 차단시켜주는 절연막층으로 구분됩니다.
그런데, 반도체가 전기적인 성질을 가지게 되려면 증착막에 이온을 주입하는 공정이 수반되어야 합니다. 이온주입 공정(Ion implantation)은 말 그대로 반도체에 전기적 성질을 띠는 입자를 회로패턴과 연결된 부분에 주입시키는 공정입니다. 이 때 이온이라 함은 붕소(B), 인(P), 비소(As) 등과 같은 불순물을 일컫는데요, 불순물을 미세한 가스입자로 만들어 원하는 깊이만큼 웨이퍼 전면에 균일하게 넣어줌으로써 일정한 전도성을 갖도록 만드는 과정입니다. 이러한 불순물 주입은 고온의 전기로 속에서 입자를 웨이퍼 내부로 확산시켜 주입하는 디퓨전(Diffusion) 공정에서도 다뤄진 바 있습니다.
지금까지 화학반응을 이용해 균일한 표면을 만드는 증착 공정과 불순물을 주입하는 이온주입 공정을 통해 부도체인 실리콘 웨이퍼가 전기적 성질을 가지는 반도체로 재탄생하는 과정에 대해 설명해 드렸습니다.
증착 공정은 박막을 얼마나 얇고 균일하게 입혔느냐가 반도체의 품질을 좌우할 정도로 중요한 공정입니다. 앞으로 미래에는 머리카락 수백만 분의 1 크기의 반도체 회로구조가 전기적 성격을 가지기 위해 더 얇고 균일하게 박막이 형성되는 증착 기술이 필요할 것으로 보입니다.
나노미터(nm, 10억분의 1미터) 크기보다 더 미세한 선폭의 공정이 주도하는 차세대 반도체 시대에도 더욱 진화하고 발전한 기술을 선도할 삼성전자의 활약을 기대해 봅니다.
☞ 반도체 8대 공정 1탄. 반도체 집적회로의 핵심재료, 웨이퍼란 무엇일까요?
☞ 반도체 8대 공정 2탄. 웨이퍼 표면을 보호하는 산화공정(Oxidation)
☞ 반도체 8대 공정 3탄. 전자산업의 혁명, 집적회로(IC, Integrated Circuit)
☞ 반도체 8대 공정 4탄. 웨이퍼에 한 폭의 세밀화를 그려 넣는 포토공정(Photo)
☞ 반도체 8대 공정 5탄. 특정 회로패턴을 구현하는 식각공정(Etching)
☞ 반도체 8대 공정 7탄. 전기를 통하게 하는 마지막 작업, 금속 배선 공정
☞ 반도체 8대 공정 8탄. 합격으로 가는 첫 번째 관문 EDS(Electrical Die Sorting)
☞ 반도체 8대 공정 9탄. 외부환경으로부터 반도체를 보호하는 패키징(Packaging) 공정
제 36화, 반도체 8대 공정 – 5.박막 증착(Deposition) 공정
제 36화, 반도체 8대 공정 – 5.박막 증착(Deposition) 공정 MANUAL / 반도체 / 디스플레이 https://blog.naver.com/ckbc6101/220966477075 안녕하세요. “빛”입니다.
요새 다시 취업시즌과 함께 바빠지다보니
포스팅 속도가 현저히 내려갔네요 죄…송…합니다 ㅎㅎ
오늘의 포스팅은 반도체 8대 공정 5번째 순서 박막 증착 공정 (Deposition) 입니다.
우선 박막(Thin Film)이란?
기계가공으로는 실현불가능한 두께인 1마이크로미터(μm) 이하의 얇은 막
을 의미합니다.
이런 박막을 웨이퍼 위에 만들어 전기적인 특성을 갖게하는 과정을 증착이라고 합니다.
박막을 만드는 방법에는 다양한 방법이 있는데
크게 물리기상증착법(PVD) 화학기상증착법(CVD) 스핀 온 글라스(SOG) 도금 으로 나누어집니다.
이렇게 박막을 만드는 방법이 다양한 이유는 필요한 스펙이 다양하기 때문이겠죠?
그래서 오늘은 증착공정을 포스팅하기에
증착시 필요한 스펙에 대해 먼저 살펴보겠습니다.
증착의 필요스펙
1. Quality(품질) :전기적 특성, 물리적 특성의 품질
2.Thickness Uniformity(두께 균일도) :웨이퍼의 규일도, 웨이퍼-to-웨이퍼 균일도, 등등
3.Step Coverage :단차에서의 일정한 두께를 유지하는지의 여부
위의 그림을 보시면 Step Coverage는 s/t이며, 균일화를 얼마나 잘했는가를 의미합니다.
단차가 있는 부분은 안쪽이 잘 안 쌓입니다.
이외에도 Aspect Ratio(종횡비)는 h/w이며, 균일화의 어려움 척도를 나타내는 수치입니다. 그리고 A/R이 클수록 균일화가 어려워집니다.
(a:Good Step Coverage b:Poor Step Coverage)
4.Filling :단차 사이 공간을 잘 채우는지
위의 그림에서 사이 공간을 증착으로 채우다보면 단차 사이 안쪽이 잘 안 채워지다보니 (c)처럼 채워지게 됩니다.
(c)를 보시면 빈 공간이 발생하게 되는데 이 공간은 Void라고 합니다.
패턴이 작아질수록 Void가 커지고 사이 간격이 좁을수록 Void가 커집니다. (Void는 결함!!)
오늘은 PVD와 CVD를 중심으로 이야기할텐데요
먼저 물리기상증착법(PVD) 금속박막 증착에 주로 사용되며, 화학반응을 수반하지 않습니다.
PVD는 Sputtering Thermal Evaporation E-beam evaporation 이 대표적입니다.
Thermal Evaporation 증착시키고자 하는 물질을 보트에 올려두고 가열함으로써 증착물질을 증발시켜 기판에 증착하는 방식입니다.
E beam Evaporation Thermal Evaporation와 거의 동일한 방식이지만 차이점은 보트에 대한 가열이 아니라 전자빔을 이용하여 증착물질을 가열하는 증착방식 이라는 것입니다.
마지막으로
Sputtering 강한 전압을 가하여 자유전자와 Ar 기체 간의 충돌로 플라즈마를 발생시키고 이에 Ar 기체가 Ar+로 이온화가 되어 (-) 전압이 가해진 Target 기판에 충돌합니다.
충돌 후 튀어나온 증착물질들이 (+) 전압이 가해진 증착기판에 증착하는 방식으로
아래와 같이 진행됩니다.
먼저, 진공상태의 Chamber 내에 자유전자(e)와 Ar기체가 존재합니다.
Target에는 (-) , 증착 기판에는 (+) 전압이 가하면 자유전자들은 (+)극인 기판쪽으로 이동하면서 Ar과 충돌을 하게됩니다.
이때, 자유전자가 (+)극인 기판쪽으로 이동을하면서 이온화가 될정도의 충분한 에너지를 받지 못하면 다른 원자의 이온화에 관여하여 플라즈마를 발생시키게 되고,
충분하게 가속이 되어 이온화를 할 충분한 에너지를 받게 되면 Ar이 이온화가 되어 Ar+와 자유 전자를 또 내놓게 됩니다.
내놓은 자유전자는 또 기체인 Ar과 충돌이 계속 일어나고, Ar+로 이온화가 되면 (-)전압의 Target 기판으로 끌려가게 됩니다.
이후, Ar+가 Target쪽으로 가속되면서 Ar+가 Target을 때리고, Target의 물질을 분리시킵니다. (Ar+는 Target과 충돌 후 Target에서 전자를 얻어 중성이 됩니다.)
튀어나온 금속원자(Target 물질)는 기판쪽으로 가서 증착이 됩니다.
어때요? 그림 자료가 설명이 잘 되어 있어서 이해가 잘 되셨을거라 생각합니다.
이번에는 화학기상증착법(CVD)에 대해서 알아보겠습니다.
CVD는 가스의 화학 반응으로 형성된 입자들을 외부 에너지가 부여된 수증기 형태로 쏘아 증착시키는 방법 (도체, 부도체, 반도체의 박막 증착에 모두 사용 가능)
대표적으로 APCVD, LPCVD, PECVD, HDPCVD, ALCVD 이 있습니다.
이외에도 더 있지만 5개만 배워도 머리가 아프죠…
우선, CVD는 아래와 같은 단계로 진행됩니다.
증착 단계 그림을 보시면서 이번엔 아래 그래프를 봐주시죠.
위의 표를 보시면 CVD는 높은 온도 영역에서와 낮은 온도 영역에서 증착 속도에 영향을 주는 Main요소가 다릅니다.
높은 온도 영역 낮은 온도 영역 확산에 의존 (Mass Transfer Controlled) 반응에 의존 (Reaction Controlled) -온도가 증가하면 화학 반응속도가 급격하게 증가해(k가 증가) 확산 속도가 증착 속도에 영향을 주는 Main 요소가 됩니다. (반응 후 새로운 확산 기체가 표면에 오기까지 대기) -Quality ↑, 속도 ↑ – 기체의 확산 속도가 일정(h가 일정)하기에 가스가 지나가면서 실리콘에 닿는 부분에서 발생하는 반응성이 증착 속도에 영향을 주는 Main 요소가 됩니다.
그럼 이제 CVD의 종류를 하나씩 알아보겠습니다.
1.APCVD Atmospheric Pressure CVD
이는 대기압 CVD이며, 특징은 Chamber는 가열하지 않습니다. (Cold Wall reactor) 대신 Chamber 외부의 RF 인덕션 코일을 가열하여 웨이퍼에 열을 전달하는 방식입니다.
위의 사진은 Chamber 내부의 웨이퍼 정렬방식인데 경사가 기울어져있는 것을 볼 수 있습니다.
이는 평면에서는 기체의 흐름이 먼저 닿는 왼쪽과 나중에 닿는 오른쪽의 박막의 두께가 일정하지 않아,
이를 일정하게 해주기 위해 약간 경사를 주는 것입니다.
하지만, 웨이퍼 Size가 커지면서 위와 같은 방법도 균일도의 한계가 발생하기 때문에 최근에는 사용하지 않는 방법입니다.
박막 두께를 일정하게 해주기 위해 위의 사진처럼 위에서 기체를 분사하는 경우도 있습니다.
2.LPCVD Low Pressure CVD
이는 저기압 CVD이며, 압력이 내려감에 따라 기체 간의 충돌이 줄어들어 확산이 많이 일어나게 됩니다.
앞서 보여드렸던 표를 보시면 확산이 많이 일어날수록 증착속도가 빨라짐 을 알 수 있습니다. (→ 온도↑ → 확산↑ → 증착↑) 온도와 증착은 비례 →Control 하기 쉬워진다.
LPCVD는 3가지 방식으로 나누어집니다.
수평방식 (Horizon Type) – Batch type 수직방식 (Vertical Type) – Batch type 단일웨이퍼방식 (Single Wafer Type) Chamber 내 균일한 온도 (Chamber 자체를 가열) 자동화가 용이 (기계가 웨이퍼를 들고 옮길 때 가로로 놓인 웨이퍼가 용이) 미세화된 공정에 용이
Batch-type System : 한번에 여러가지를 동시에 해내는 시스템
※몇가지 물질 (poly Si, SiO2, Si3N4) 외에는 전부 Single Wafer type에서만 증착 가능합니다.
3.PECVD Plasma Enhanced CVD
PECVD는 가장 많이 사용되는 CVD 중 하나입니다.
이는 저온(약 400도)에서도 공정이 가능하기 때문인데요. (고온 공정시 웨이퍼 위의 Al 도선이나 유리기판이 녹음)
저온 공정이 가능한 요인은 바로 플라즈마 입니다.
플라즈마 상태란?
분자상태로 존재하는 기체를 강한 전압에 의해서 이온으로 나누어 놓은 상태 (이온으로 이루어진 기체)
반응시킬 기체를 주입하고 높은 전압을 수직으로 걸어줍니다.
수직으로 전압을 걸어주는 이유는 플라즈마 상태로 바꾸기 위함입니다.
그러면 플라즈마 상태로 이온화된 기체들은 서로 화학반응을 하여,
원하는 물질은 기판에 고르게 쌓이고
나머지 이온들도 결합하여 기체로 배출되게 됩니다.
어때유? 쉽쥬우??
이후부터는 Step Coverage를 높이기 위한 방법으로써 ————————————————————————————— 4.HDPCVD High Density Plasma CVD
플라즈마의 농도가 높아질수록 증착 속도가 높아집니다.
그런데 여기서 유의해야할 것은 지난 식각공정 시간에서 플라즈마는 식각으로도 쓰인다는 거 기억하시나요?
그렇습니다. 플라즈마는 증착, 식각이 둘 다 동시에 이루어짐으로
이 둘의 속도를 조율하여 동시에 사용(증착, 식각)하는 것이 HDPCVD의 열쇠입니다.
증착, 식각을 번갈아가며 반복
식각으로 사이 공간을 확보하면 증착하기가 더 쉬워지기 때문에 Void가 발생할 확률이 줄어듭니다.
다음 Step Coverage를 향상시키는 방법인
5.ALCVD Atomic Layer CVD
AB가 증착시키고자 하는 물질일 때,
AX(g) + BY(g) → AB(s) + XY(g)
의 반응식을 이용하는 방식입니다.
기판에 붙어있는 것만 반응하기 때문에 위의 사진 속 과정을 계속 반복해서 균일화해주는 것입니다.
(사이사이 빈 공간이 있지만, 평균적으로 면적당 균일도는 ↑)
그렇게 되면 아래와 같이 ALCVD에서는
속도(거리)차에 의한 layer차가 없이
균일한 layer를 증착할 수 있습니다.
하지만 단점으로는 한층 한층 쌓아야하기 때문에 과정이 매우 느리다는 점. 그리고 그렇기 때문에 얇은 필름 요구시에만 사용된다는 점.
네, 지금까지 다양한 CVD의 종류를 살펴보았습니다.
표로 한번에 정리 해볼까요?
장점 단점 용도 APCVD 저렴 간단 빠른 증착 속도 균일도를 조절하기 어렵다 (Step Coverage가 나쁨) 저온, 평평한 산화막 LPCVD 고품질 필름 높은 생산량 고온 공정 (CVD 중 가장 높다) 느린 증착 속도 Funace Type: Poly-Si, SiO2, Si3N4 Single Wafer Type: 나머지 물질 PECVD 저온 증착 가능 빠른 증착 속도 저품질 필름 IMD 증착 Passivation 증착 HDPCVD Gap filling 특성 우수 저온 공정에서 고품질 산화막 플라즈마 데미지 불균일한 증착 (전기장의 퍼지는 성향) Shallow Trench Isolation(STI)에 적합 IMD 증착 ALCVD 고품질 필름 & Step Coverage nm 단위의 박막 두께 조절 가능 낮은 생산량 게이트 유전막 증착 Interconnect 증착
추가로 높은 온도에서 퀄리티 좋은 박막이 생성되는 이유!!
화학반응으로 이루어진 생성물이 높은 온도로 인해 뜨거워진 기판 내부를 이리저리 움직일 수 있는 에너지를 제공받게 됩니다.
그리고 이렇게 움직이다보면 에너지적으로 가장 안정한 위치에 결합될 확률이 증가되면서,
결과적으로 높은 온도에서 박막을 성장시키면 퀄리티 좋은 박막을 형성할 수 있습니다.
하지만, 기체의 확산 속도는 크게 변하지 않아 박막 증착 속도의 변화는 없습니다.
더불어 기체의 확산속도를 높여 APCVD보다 더 높은 온도에서 더 빠르게 박막을 성장시킬 수 있는 방법이 LPCVD입니다.
딱히 따로 챕터를 꺼내서 정리할 필요는 없지만
마지막으로 PVD와 CVD를 비교해보고자 Ch 4. 내용정리를 준비했습니다.
위의 그림(표)에서는
ALCVD를 같이 비교하기 위해 ALD로 따로 분류를 해주었습니다.
지금까지 반도체 8대 공정 5번째, 증착공정에 대해서 알아보았습니다.
어마어마한 분량이었네요…ㄷㄷ
제일 공을 많이 들인 포스팅이 아니었나 싶습니다.
그럼 오늘은 여기까지
자료출처: http://samsungsemiconstory.com 서울대학교 반도체공동연구소 인쇄
웨이퍼에 균일한 ‘도화지’를 입히는 사람들_Thinfilm기술담당
반도체 공정에서 ‘박막(Thinfilm) 공정’은 웨이퍼(Wafer) 표면에 분자 또는 원자 단위의 물질로 1㎛(마이크로미터) 이하의 매우 얇은 막을 입히는 과정을 의미한다. 이 막은 전기가 통하지 않는 부도체 상태의 웨이퍼가 전기적 특성을 지닐 수 있게 해줘, 이후 공정에서 회로 패턴과 구조가 잘 구현할 수 있도록 도와주는 ‘도화지’ 역할을 한다. SK하이닉스에서 이 업무를 담당하고 있는 조직이 제조/기술담당 산하 Thinfilm기술담당이다.
뉴스룸은 Thinfilm기술담당 구성원 중 청주NAND M11 CVD기술팀, 청주NAND M11 PVD기술팀 구성원들을 만나 현재 맡고 있는 업무 전반과 각 팀에서 바라는 인재상에 대해 들어봤다.
공정 조건에 맞는 얇은 막을 균일하게 증착시키는 ‘Thinfilm 공정’
박막 공정의 목적은 웨이퍼에 전기적 특성을 부여해 다음 공정을 위한 ‘판’을 깔아주는 것이다. 이를 위해 공정 조건에 맞게 박막 두께의 정도, 굴절률(Refractivity), 흡수율(Absorptivity) 등을 계산해 막을 증착하고 있다. 무엇보다 균일한 막을 웨이퍼에 고르게 증착하는 기술이 중요한데, 박막의 균일도에 따라 이후 포토(Photo) 및 식각(Etch) 공정에서 구현되는 회로 패턴의 정밀도가 좌우되기 때문이다.
증착 방식으로는 ‘물리적 기상 증착 방법(Physical Vapor Deposition, 이하 PVD)’과 ‘화학적 기상 증착 방법(Chemical Vapor Deposition, CVD)’이 주로 사용된다.
PVD는 금속판에 물리적 반응을 일으켜 금속 물질을 이온 상태로 웨이퍼에 입히는 기술이다. 이 방식은 저온과 고진공 상태에서 공정이 진행돼 불순물로 인한 오염이 적고, 증착이 빠르다는 장점이 있다. 주로 금속막(Metal Layer)를 증착하는 데 사용하는데, 이 막은 웨이퍼의 전기적인 힘과 신호를 전달하는 역할을 한다.
PVD에는 대표적으로 ‘스퍼터(Sputter)’ 방식이 이용되고 있다. 진공 상태의 챔버(Chamber)에 아르곤 가스를 주입한 후 높은 전압을 걸면 플라즈마(Plasma) 상태가 된다. 이때 마이너스 직류 전압을 걸어 아르곤 원자를 양이온으로 바꾼 뒤 이를 금속판에 충돌시키면 금속 성분이 떨어져 나오는데, 이를 웨이퍼에 증착하는 방식이 스퍼터 방식이다.
CVD는 기체(Vapor)에 열 혹은 플라즈마를 가해 화학반응을 유도한 뒤, 이를 웨이퍼에 증착하는 기술이다. PVD보다 스텝 커버리지(Step Coverage, 박막의 수직-수평 방향 간 증착 비율의 균일도)가 더 높다는 특징이 있다. 주로 절연막(Dielectric Layer)을 증착할 때 사용한다. 또한 포토 공정에서 패턴을 그릴 때 난반사를 제어하는 ARC(Anti-Reflective Coating)를 증착하거나 식각 공정에서의 하부 레이어(Layer)를 보호하기 위한 하드마스크(Hard Mask)를 웨이퍼 위에 올릴 때도 CVD 기술이 활용된다.
CVD는 공정이 이뤄지는 환경적인 조건에 따라 ‘APCVD(Atmospheric Presssure CVD)’, ‘Thermal CVD’, ‘PECVD(Plasma Enhanced CVD)’, ‘HDP-CVD(High Density Plasma CVD)’ 등 총 네 가지 방식으로 다시 분류된다.
APCVD는 대기압 상태에서 증착을 진행하는 방식이다. 처리율(Throughput)이 좋고 장치 구조가 간단하지만, 진공도가 낮아 스텝 커버리지가 나쁜 편이다.
Thermal CVD는 고온 환경에서 열에너지를 이용하는 증착법으로 APCVD 대비 박막의 균일도가 높다. 하지만 증착 속도가 느리고 고온 환경에 따른 위험요소를 고려해야 한다.
PECVD는 플라즈마의 라디칼(Radical, 활성종)로 화학반응에 필요한 활성화 에너지를 감소시켜, 낮은 온도에서 박막을 형성하는 방식이다. 처리율이 높고 스텝 커버리지가 양호한 편이다.
HDP-CVD는 챔버 내에서 증착과 식각을 동시에 진행하는 방식으로, 저압과 고밀도 플라즈마 상태에서 증착이 진행된다. 이 방식은 꺼진 부분(Void)을 갭필(Gap-fill, 공극을 채우는 것)하는 데 활용도가 높다.
“기술혁신을 통해 최고의 양산 기술력 확보” Thinfilm기술담당의 핵심 가치
Thinfilm기술담당 산하에는 증착 업무를 실질적으로 담당하는 CVD기술팀과 PVD기술팀이 FAB별로 이천, 청주에 각각 배치돼 있다. 우시 FAB에서는 CVD와 PVD를 따로 구분하지 않고 Thinfilm기술팀이 관련 업무를 모두 맡고 있다. 여기에 공정 지원 업무를 담당하는 기술혁신팀과 산포개선팀을 더해 총 7개 팀을 운영 중이다.
PVD기술팀에서는 스퍼터 방식뿐만 아니라 반응성 이온식각(Reactive Ion Etch, RIE)1), 다마신(Damascene)2) 방식 등 다양한 방식을 활용해 PVD를 진행하고 있다. 이는 각 공정별로 가장 적합한 박막을 증착하기 위한 노력으로, 최근에는 셀 하부의 금속선(Metal Line)을 안정적으로 형성하기 위한 증착 기술도 개발 중이다.
1) 반응성 이온식각(Reactive Ion Etch, RIE) : 전기가 통하는 길을 만드는 금속 배선 공정 중 하나. 알루미늄(Al) 금속막을 증착시킨 후 포토 공정과 일부 AI 식각을 거친 뒤, 이산화규소(SiO2)의 비금속막을 증착하는 방식.
2) 다마신(Damascene) : 전기가 통하는 길을 만드는 금속 배선 공정 중 하나. 이산화규소(SiO2) 비금속막을 증착해 포토 공정과 식각을 거쳐 패턴을 형성해, 내부에 금속막을 증착한 뒤 CMP(Chemical Mechanical Polish) 공정을 거쳐 각각의 독립된 금속선(Metal Line)을 만드는 방식.
CVD기술팀에서는 HDP-CVD와 PECVD 방식을 활용해 절연막을 안정적으로 증착하는 업무를 수행하고 있다. 이와 함께 후속 공정의 효율을 높이는 데 필요한 ARC 및 하드마스크 증착 업무도 담당하고 있다. 최근에는 박막을 균일하게 만들기 위해 산화막과 질화막을 번갈아 적층하는 기술도 확보 중이다.
두 팀 모두 업무에 특성에 따라 공정 파트와 장비 파트로 역할이 세분화돼 있다. 공정 파트에서는 웨이퍼가 안정적으로 박막에 증착할 수 있도록 공정을 최적화하고 있으며, 공정 결과값(Response Data), 불량 데이터(Defect Data) 등을 분석해 산포를 개선하는 업무도 진행하고 있다.
장비 파트는 장비를 유지관리하고 성능을 개선하는 역할을 맡고 있다. 장비 사용 이력을 관리하며 박막의 불량 이슈(Issue)에 대응하는 업무와 생산 계획에 따라 장비 셋업(Set-Up)을 하거나 이설하는 업무도 장비 파트가 총괄하고 있다.
기술혁신팀은 각 FAB의 장비에서 얻은 다양한 데이터를 활용해 장비를 안정화하는 업무를 담당하고 있다. 산포개선팀은 각 FAB의 공정 산포를 개선하는 업무를 맡고 있다. 두 팀 모두 FAB별로 나뉘어져 있는 팀들을 지원하며, 제품의 수율을 향상하는 데 이바지하고 있다.
이처럼 공정별로 팀이 나뉘어져 있지만, 목표는 하나다. 기술혁신을 통해 최고의 양산 기술력을 확보하는 것. 이를 위해 서로 지속적으로 소통하며 공정 기술을 개선해가고 있다.
[Q&A] Thinfilm기술담당 실무자에게 듣는 직무 Tip뉴스룸은 SK하이닉스의 Thinfilm기술담당 실무자들을 만나 업무에 필요한 역량과 자질에 대해서도 들어봤다.
▲ 청주 NAND M11 PVD 기술팀 김현도 TL
Q. 현재 어떤 업무를 맡고 있나?
청주NAND M11 PVD기술팀에서 공정 엔지니어로서 박막의 품질을 높이는 업무를 맡고 있다. 이를 위해 팀에서 진행하는 PVD 공정을 모두 모니터링해 인라인(In-Line, 제조 라인의 각종 작업을 하나의 연속공정으로 처리하는 것)에 이상이 발생하는지 확인하고 있으며, 결함 발생 시 공정 결과값과 불량 데이터를 분석해 원인을 파악하고 산포를 개선하고 있다.
Q. 업무에 필요한 역량은 무엇인가?
PVD 기술을 잘 이해하고 있어야 한다. 반도체 소재의 특성과 진공에서 이뤄지는 물리학적 원리에 대해 공부하면 좋다. 반도체 제조 과정에서도 빅데이터(Big Data)를 활용하고 있기 때문에 툴(Tool) 사용법과 가공한 데이터 해석을 하기 위한 통계적 지식을 갖추는 것도 중요하다.
Q. 힘들 때는 언제인가? 또 이를 어떻게 극복했나?
생산량 문제와 품질 문제가 상충할 때 가장 큰 어려움을 느낀다. 생산을 무리하게 늘리면 품질에서 이슈가 생기기 때문이다. 이를 해결하기 위해 타 FAB의 백업(Back Up) 평가와 생산량 증대 실험을 통해 생산량을 늘리고, 데이터를 꼼꼼히 관리해 품질 문제가 발생하지 않게 노력하고 있다. 그리고 불량 분석에 활용할 새로운 데이터를 찾으려고 노력 중이다.
Q. 업무의 매력은 무엇이라고 생각하나?
문제가 발생했을 때 원인을 찾기 위해 팀원 혹은 유관 부서 구성원과 끊임없이 소통하고 원인을 찾아나가는 과정이 즐겁다.
Q. 팀의 전반적인 분위기는 어떤가?
자신의 의견을 자유롭게 이야기하는 분위기이다. 도움이 필요한 일이 생기면 동료들과 최대한 협력하고, 각자의 의견을 스스럼없이 공유하고 있다. 이렇게 의견을 나누는 과정을 통해 시야가 더 넓어지고 성장하는 것 같다.
Q. 이 업무에 필요한 신입사원의 자질은 무엇인가? 미래의 후배들에게 전하고 싶은 메시지가 있다면?
책임감과 섬세함이 필요하다. 얇은 막을 다루는 공정을 진행하는 업무 특성상 공정 사고 위험에 자주 노출되는 편이다. 꼼꼼하게 업무를 끝까지 책임지는 자세가 중요하다. 또한 팀 또는 유관부서와 협업이 많은 만큼, 다른 사람과 잘 소통할 수 있는 성격이 유리하다.
▲ 청주 NAND M11 PVD 기술팀 김민호 TL
Q. 현재 어떤 업무를 맡고 있나?
청주NAND M11 PVD기술팀에서 PVD 공정에 사용되는 티타늄(Ti)와 질화티탄(TiN) 가스를 다루는 장비 업무를 담당하고 있다. 장비를 운용하고 생산량에 맞춰 작업을 관리하는 PM(Project Management) 업무를 진행하고 있으며, 웨이퍼에 불량이 발생했을 시 공정 엔지니어와 협업해 문제를 해결하고 있다.
Q. 업무에 필요한 역량은 무엇인가?
반도체 장비는 파워, 온도, 압력, 흐름 등의 조건이 여러 상황에 따라 각각 다르게 접목된다. 다방면의 지식을 갖고 접근하는 역량이 필요하다. 학창시절에 전공수업을 통해 기초지식을 잘 쌓아두면 큰 도움이 된다. 또한, 장비의 온도/압력 등 각종 센서에서 모니터링된 파라미터(Parameter)를 통해 얻어진 정보들을 유의미한 데이터로 가공할 수 있는 데이터 분석 역량도 갖추면 장비 파트를 업무를 수행하기에 수월하다.
Q. 힘들 때는 언제인가? 또 이를 어떻게 극복했나?
장비를 운용하고 문제를 해결하는 과정에서 많은 사람과 협업이 이뤄진다. 실제 라인에서 문제가 발생했을 때 현장과 사무실 간의 원만한 소통이 이뤄져야 상황에 맞는 적절한 조치가 가능해진다. 이에 적절한 상황에 맞는 핵심 정보를 전달하기 위해 SKHU(SK하이닉스 교육 시스템)의 강의와 매주 목요일 제조기술 조직에서 진행되는 강의를 통해 반도체에 관한 역량을 채우고 있다.
Q. 업무의 매력은 무엇이라고 생각하나?
새로운 가설을 세워 어려운 난제를 해결했을 때다. 공정 진행 중에 웨이퍼에 문제가 생기면 챔버 내부를 확인할 수 없다. 이에 여러 가지 근거를 바탕으로 가설을 세워 개선해나가고 있다. 과정은 어렵지만 해결한 순간이 가장 짜릿하게 다가온다.
Q. 팀의 전반적인 분위기는 어떤가?
PVD기술팀은 개개인의 의견을 존중하는 열린 분위기이다. 이러한 분위기 속에서 유연한 사고를 갖고 업무를 수행할 수 있었고, 덕분에 업무 효율도 높일 수 있었다.
Q. 이 업무에 필요한 신입사원의 자질은 무엇인가? 미래의 후배들에게 전하고 싶은 메시지가 있다면?
유연한 사고가 가장 필요한 자질이라고 생각한다. 반도체 제품이 점점 고도화되면서 기존 방식만으로는 문제가 개선되지 않는 경우가 종종 있다. 이럴 때는 처음부터 가설을 세우고 접근해야 해 경직된 사고로는 난제들을 해결하기 어렵다. PVD기술팀에 입사할 신입사원이라면 이 과정을 힘들다고 생각하기보다 하루하루 새로운 문제에 직면하고 배워 전문가가 되는 과정이라고 생각하면 좋겠다.
NAND M11 CVD 기술팀 심승욱 TL
Q. 현재 어떤 업무를 맡고 있나?
청주NAND M11 CVD기술팀에서 공정 엔지니어로 일하고 있다. 제조 생산 계획에 따른 공정별 이력을 관리하면서 인터록(Interlock)을 점검하는 역할을 맡고 있다. 다음 세대의 제품이 개발되거나 신규 장비가 이관됐을 때, 유관 부서와 협업을 통해 공정을 셋업하는 것도 주요 업무 중 하나다.
Q. 업무에 필요한 역량은 무엇인가?
장비 간 데이터 유의차를 정확하게 분석할 수 있는 역량이 반드시 필요하다. 수율 향상을 위해서는 장비 간 물성차가 없는 균일한 박막 증착이 필수 불가결하기 때문이다. 이를 위해 증착이 진행된 이후 수집된 결과값을 빠르게 팀 내 공유를 할 수 있는 분석력을 갖춰야 한다.
Q. 힘들 때는 언제인가? 또 이를 어떻게 극복했나?
공정에서 문제가 발생했을 때, 정확한 원인을 찾기 어려울 때가 가장 힘들다. 원인을 파악하기 위해 연계 공정 부서와 협업하고 있으며, SK하이닉스 빅데이터 분석 시스템을 적극 활용해 문제에 대해 파악하고 재발 방지를 위해 조건에 맞는 인터록을 구현하고 있다.
Q. 업무의 매력은 무엇이라고 생각하나?
혼자의 힘으로 불가능한 일을 협업을 통해 그 이상의 결과를 내는 것이 업무의 매력이다. 공정 엔지니어 특성상 결과값을 통해 유관부서와 협업을 진행할 경우가 많다. 그럴 때마다 타 공정에 대한 지식도 얻고, 문제도 해결하는 두 마리 토끼를 잡으며 업무를 수행하고 있다.
Q. 팀의 전반적인 분위기는 어떤가?
외부에서 바라보는 반도체 제조업의 이미지는 딱딱하다는 것이다. 하지만 CVD기술팀은 신입사원들의 신선한 아이디어를 적극 수용하는 수평적인 조직이다. 개인 여가 생활을 지킬 수 있는 환경으로 워라밸도 잘 갖춰져 있다.
Q. 이 업무에 필요한 신입사원의 자질은 무엇인가? 미래의 후배들에게 전하고 싶은 메시지가 있다면?
문제를 해결하려는 열정과 도전정신만 있다면 입사 후 어떠한 어려움도 모두 헤쳐나갈 수 있다고 믿는다. 특히 Thinfilm기술담당은 신입사원 교육체계가 잘 갖춰져 있어 점점 성장하는 자신의 모습을 볼 수 있을 것이다.
▲ 청주 NAND M11 CVD 기술팀 조태욱 TL
Q. 현재 어떤 업무를 맡고 있나?
청주NAND M11 CVD기술팀의 장비 파트에서 일하고 있다. 양산 장비의 안정적인 운용을 위해 PM 계획을 수립하고 있으며, 신규 장비를 셋업 하거나 잉여 장비를 이설하는 업무도 맡고 있다. 또한 장비에서 발생하는 이슈를 검토해 유관 부서와의 협업하며, 문제를 개선하는 업무를 담당한다.
Q. 업무에 필요한 역량은 무엇인가?
장비 파트의 업무를 수행하는 데에는 ‘꼼꼼함’이 중요하다. 장비에서 발생하는 문제를 살펴보면 아주 사소한 부분을 놓쳐서 생기는 경우가 있다. 이런 일이 발생하지 않도록 장비가 잘 운용되고 있는지 섬세하게 확인해야 한다.
Q. 힘들 때는 언제인가? 또 이를 어떻게 극복했나?
장비의 고질적인 문제를 해결하려면 시간과 인력이 많이 소요될 뿐만 아니라 해결 이후에도 무엇이 원인인지 정의하기 힘들다. 이런 문제를 해결하기 위해 장비의 이력과 데이터를 꾸준히 정리하고, 문제 접근방식에 우선순위를 정하고 있다. 이와 함께 생산 라인에 입실해 직접 장비를 보고 만지며 개선해 나가고 있다.
Q. 업무의 매력은 무엇이라고 생각하나?
새로운 장비를 FAB에 셋업하는 업무를 진행한 적이 있다. 무에서 유를 창조하듯이 장비 하나하나를 준비해 무사히 마칠 수 있었다. 이 장비들이 생산에 기여하는 모습을 보고 뿌듯함을 느꼈다.
Q. 팀의 전반적인 분위기는 어떤가?
유연근무제 도입 이후 더 자율적인 업무 환경이 조성됐다. 정해진 기준 내에서 탄력적으로 업무를 볼 수 있어 일과 생활의 균형을 잘 맞출 수 있다.
Q. 이 업무에 필요한 신입사원의 자질은 무엇인가? 미래의 후배들에게 전하고 싶은 메시지가 있다면?
배우려는 의지와 성실한 모습만 보여주면 좋을 것 같다. 입사를 준비하기까지 해온 노력과 경험이 업무를 수행하는 데 밑바탕이 될 것이다. 자신감을 갖고 앞으로 나아가길 바란다.
[World Tech] 반도체 8대 공정 ⑤박막증착 공정
[월드투데이 이예찬 기자] 반도체 칩에는 수많은 층이 존재하여 마치 고층 건물처럼 높고 복잡한 구조를 이루고 있다.이러한 구조를 형성하기 위해서는 앞서 소개했던 포토공정과 식각공정을 여러 번 반복하게 된다. 이때 회로 간의 구분과 연결, 보호 역할을 하는 1마이크로 미터(μm) 이하의 얇은 막을 박막(Thin Film)이라고 한다.
[사진=pexels]증착(Deposition)이란 반도체 소자를 구동하기 위해 필요한 다양한 물질을 얇은 두께의 박막으로 형성하는 과정을 뜻한다. 물질을 증착하는 방법에는 크게 물리적인 방법인 PVD(Physical Vapor Deposition)과 화학적인 방법인 CVD(Chemical Vapor Deposition) 2가지로 나눌 수 있다.
물리적 증착법(PVD)
물리적 증착법은 주로 금속 박막의 증착에 사용되며 화학반응이 수반되지 않는 증착법이다. 물리적 증착법에는 Thermal evaporation, E-beam evaporation, Sputtering이 있다.
▼Thermal evaporation
Thermal evaporation은 증착 시키고자 하는 물질을 진공 Chamber에 넣고 가열시켜 증착 물질을 증발시켜 기판에 증착하는 방법이다. 진공에서 진행하는 이유는 다른 불순물이 기판에 증착되는 것을 막기 위함이다. 단원소 물질을 증착하고자 할 때 주로 사용된다.
다른 물리적 증착법에 비해 장비의 비용이 저렴하고 증착 과정이 단순하다는 장점이 있지만 이 방식은 모든 방향으로 물질이 동일하게 퍼지는 등방성을 가지고 있기 때문에 증착 물질이 단차에서 일정한 두께(균일도)를 유지하기가 힘들다.
▼E-beam evaporation
E-beam evaporation 방식은 Thermal evaporation 방식과 동일한 방법으로 물질을 가열하여 증발시킨 후 기판에 증착시키는 방법이다. 차이점은 직접적으로 가열하는 것이 아닌 전자빔(E-beam)을 이용하여 증착 물질을 가열하는 방식이다.
마찬가지로 일정한 균일도를 유지하기 힘들지만 높은 에너지의 전자빔을 이용해 플라즈마 상태를 만들어주면 균일도를 향상시킬 수 있다.
증착 속도가 빠르고 높은 용융점을 갖는 시료 또한 증착이 가능하고 높은 흡착력을 갖는 장점이 있다. 하지만 높은 에너지의 전자는 전자가 산란되는 원인이 되기 때문에 높은 진공도를 유지해야 한다는 단점이 있다.
▼Sputtering
진공 상태의 Chamber에 비활성 기체인 Ar을 채워주고 고전압을 걸어주면 (-) 극에서 전자가 방출되어 (+) 극으로 가속되면서 Ar 원자와 충돌하게 된다. 이때 Ar이 이온화되고 가속되어 증착하고자 하는 타겟과 충돌하여 타켓 물질이 분리되어 기판에 증착이 된다.
Sputtering은 가해주는 전압의 종류에 따라 DC(직류) Sputtering과 RF(교류) Sputtering으로 나뉜다. DC Sputtering은 주로 금속과 같은 도체에 사용하며 RF Sputtering은 반도체에 부도체에 주로 사용된다.
이 방식은 높은 용융점을 갖는 물질도 증착이 가능하며 두께 조절이 상대적으로 용이하다는 장점이 있다.
화학적 증착법(CVD)
가스의 화학 반응으로 형성된 입자들을 외부 에너지가 부여된 수증기 형태로 쏘아 증착시키는 방법으로 도체, 부도체, 반도체의 박막 증착에 모두 사용할 수 있다는 장점이 있다.
현재 반도체 공정에서 주로 사용하고 있는 방법으로 화학적 증착법은 사용하는 외부 에너지에 따라 Thermal(열) CVD, Plasma Enhanced(플라즈마) CVD, Photon(광) CVD로 분류할 수 있다.
[사진=pexels]이 중 PECVD(Plasma Enhanced CVD)는 저온에서 형성이 가능해 고온 공정이 불가능한 반도체 후속 공정에서 유리하고 두께 균일도를 조절할 수 있으며 대량 처리가 가능하다는 장점이 있다.
또한 기판의 형태가 복잡하더라도 균일한 증착이 가능하고 기판 상의 특정한 영역에 선택적 증착이 가능하다. 이러한 이유로 화학적 증착법 중 PECVD가 가장 많이 이용되고 있다.
박막을 얼마나 얇고 균일하게 입혔는지에 따라 반도체의 품질이 좌우되므로 박막증착공정은 상당히 중요한 공정이라고 할 수 있다. 다음 금속 배선 공정은 이전 공정들을 통해 만든 소자들을 상호 연결하여 회로의 기능을 갖도록 하는 공정이다.
[반도체 8대공정] 5. 박막 증착 공정
728×90
1. 박막 증착(Thin film Deposition)
1) 박막 증착이란?
– 원하는 물질을 기판에 붙이는 것을 증착(Deposition)이라고 한다.
2) 왜 박막(Thin film)을 쓰는가??
bulk상태에서 얻기 어려운 특성을 얻기 위해. 여러가지 특성을 혼합하기 위해 세상에 존재하지 않는 특성을 구현하기 위해 나노 단위 소자를 만들 때 다양한 기능을 하는 layer를 얻기 위해
2. PVD란?
– PVD(Physical Vapor Deposition)란 열 또는 충격과 같은 물리적 반응을 통해 박막을 표면에 증착하는 방식이다.
3. Thermal Evaporation (열 증착법)
1) 증착이 일어나는 연소실(챔버)을 진공으로 만들어준다.
2) 증착 하고자 하는 시료에 저항열을 가하여 기체로 만든다.
3) 기판에 도착한 기체는 차가운 기판을 만나 응축된다.
4) 기체 문자들이 응축을 거듭하며 박막을 형성한다.
4. E-beam Evaporation
1)열 증착 법의 한계
– 열 증착 법은 Furnace 자체를 가열하므로 부분적인 증발이 어려움.
– 가할 수 있는 온도의 한계가 존재
2) 전자 빔 증착 법(E-beam Evaporation)
필라멘트애서 발생한 e-beam을 사용해 소스를 Local하게 가열한다. 전자 beam을 정밀하게 조절하기 위해 전자석과 영구자석 이용 물에 의해 냉각되는 수냉로를 사용하기 때문에 용기로 부터 불순물이 섞이지 않음 높은 균일성을 띄는 박막을 높은 증착률로 증착 가능
5. Sputtering
1) Sputtering 과정
Target 물질을 음극에, 기판을 양극에 위치시킨다, 비활성 기체인 아르곤(Ar)을 주입한 후 전극에 전압을 가한다. 전자는 음극(Cathode)에서 나와 양극(Anode)쪼으로 이동한다. 이 과정에서 전자는 Ar과 강한 충돌을 하여 이온화 시켜 플라즈마 상태가 됨. 전자를 잃어 이온화된 Ar+ 이온은 (+) 전극을 띄기 때문에 음극으로 가속되어 충돌해 Target 물질의 원자 결합을 끊는다. 원자 간의 결합이 끊어져 튀어나온 전자와 Ar+이온이 결합해 중성상태가 되어 더 이상 음극에 끌리지 않게 된다. 떨어져 나온 원자나 이온들은 기판에 증착 되면서 박막을 형성함.
2) DC / RF Sputtering 차이
DC sputtering : 전극이 한 방향으로만 가해져 부도체에서는 전자가 떨어져 나오지 않아 이온은 음극에 잡혀 점점 쌓이면서 새로 충돌하는 이온들을 밀어내 결국 중성상태가 되게 만들어 부도체에 사용 불가
RF sputtering : 전극이 주파수에 따라 변하며 음극에서 양극으로 바뀌며 부도체에 달라붙지 않고 연속적으로 충돌을 일으켜 부도체로도 증착이 가능.
1. CVD란?
– CVD(Chemical Vapor Deposition)란 형성하고자 하는 박막 재료를 구성하는 원소를 포함하는 가스를 기판 위에 공급해 기상 또는 기판 표면에서 화학적 반응으로 박막을 기판에 형성하는 방법.
2. CVD 장점
– PVD보다 표면 접착력이 10배 높음
– 대부분의 표면에 적용 가능하므로 활용도가 높음
– 도체, 부도체, 반도체 박막 증착에 모두 사용가능
– 불순물의 분포와 농도조절 가능
– 반응 가스 선택가능
– 대량생산 가능
3. CVD 단점
– 압력이 낮을수록 공정의 프로세싱 시간이 길어짐
– 고진공 상태에서 기체들의 반응속도를 유지하려면 웨이퍼 온도를 높여야 하지만, 그러면 재료 선택이 까다로워짐
– 두께 조절 컨트롤하기 어려움
– 반응 변수가 많음
– 위험한 가스의 사용
4. CVD 방식의 종류
– 열에너지 이용 방식 : APCVD(대기압), LPCVD(저기압)
– 플라즈마 에너지 이용 방식 : PECVD(저밀도 플라즈마), HDCVD(고밀도 플라즈마)
– 원자를 표면에 흡착시키는 방식 : ALCVD(원자층 증착방법)
5. CVD 원리
1) 프로세스 챔버 속으로 주입된 반응 가스가 웨이퍼 표면 위로 이동
2) 반응 가스가 표면에 흡착
3) 화학반응을 거쳐 웨이퍼 표면에 고체 상태(막)을 형성하고, 반응 부산물(Byproduct) 생성
4) 반응부산물 가스가 웨이퍼 표면으로부터 탈착하여 프로세스 챔버의 gas stream으로 증발된 후 밖으로 배출
6. ALD(Atomic Layer Deposition) 원리
1) 흡착단계 : 1차 소스(전구체)를 프로세스 챔버에 넣으면 먼저 표면 흡착이 일어난다.
2) 치환단계 : 다른 종류의 2차 소스(반응체)를 넣으면 1차 흡착된 물질과 화학적 치환이 일어난다.
3) 생성단계 : 최종적으로 제3의 신규물질(막)이 생성된다.
4) 배출단계 : 잔류 가스가 배출되어 결국 1개 층만 표면에 흡착되어 달라붙게 된다.
총 4 개의 단개가 하나의 사이클로 계속해서 반복하여 layer 두께를 조절할 수 있다 .
7. ALD특징
– PVD와 같은 물리적 방식이 아니고, CVD와 유사한 화학적 방식
– 갭이나 트랜치의 벽면에도 잘 달라 붙음
– 섭씨 400도 이하(200~400도)의 낮은 온도에서 공정진행이 가능
1) ALD 장점
– 자기제어반응으로 단위nano 미터급 두께 정밀히 쌓을 수 있음
– 층 내의 전체 격자가 정형적인 각을 이뤄서 질서정연하고 얇은 두께 형성
– 두께 조절에 획기적
– 낮은 온도에서 공정이 가능해 다른 막에 영향을 거의 끼치지 않음
2) ALD 단점
– 1개 사이클에 원자층이 1개 층 씩만 쌓여 속도가 느림
– 저온에서 진행하여 막의 물성이 떨어짐
– 1차 소스와 2차 소스들을 선택하는 데 한정적
3) ALD의 활용
– DRAM의 캐패시터
– 게이트 옥사이드
– 메탈 베리어(Metal Barrier)
– NAND의 3D를 구성하는 가장 중요한 절연 막/금속
728×90
반도체 8대공정 4탄, 박막(Thin Film)증착(Deposition)공정 개념정리
반도체 8대공정 4탄, 박막(Thin Film)증착(Deposition)공정 개념정리
웨이퍼 공정을 통해 탄생한 웨이퍼는 전기적 특성이 없습니다. 이 웨이퍼에 전기적 특성을 입히는 공정을 박막 (Thin Film)증착(Deposition) 공정 이라고 합니다. Deposition은 크게 2 가지 방식으로 분류할 수 있습니다. PVD(Physical Vapor Deposition)와 CVD(Chemical Vapor Deposition)입니다. 최신 반도체공정에서는 CVD 가 주로 활용 되고 있는데 그 이유는 P VD보다 표면접착력이 10 배나 높고 활용도가 높은 장점 이 있기 때문입니다.
저는 우선 PVD 방식부터 정리하도록 하겠습니다.
– PVD(Physical Vapor Deposition)
1. Thermal Evaporation
Thermal Evaporation은 Vacuum state에서 Deposition하고자 하는 물질에 열을 가해 증발시켜 웨이퍼 표면에 박막을 입히는 방식입니다. 하지만 증발한 물질은 고루 diffused 하지 않고 Isotropic하게 diffused 되므로 Step Coverage가 좋지 않습니다.
* Step Coverage : Hole이나 Gap 측벽면에 Deposition이 균일한 정도
2. E-beam Evaporation
이전 방식과 동일하지만 Deposition하고자 하는 물질에 열 대신 E-beam 을 가해 증발시키는 차이가 있습니다. 이때, 높은 에너지의 E-beam을 통해 플라즈마 상태로 만든 후 DC전압을 인가하는 방식으로 Step Coverage를 개선할 수 있습니다.
3. Sputtering
Vaccum state에서 Substrate는 +극을, Target에는 -극을 걸어준 후 비활성 Ar 가스를 주입합니다. 그 후 전압을 인가하면 +극으로 가속하는 전자와 Ar 원자가 충돌하면서 Ar+로 활성이 됩니다. 이 Ar+는 Target이 있는 -극으로 이동하여 Target과 충돌합니다. 그 결과 Target에 있는 원자들이 방출되어 +극에 있는 Substrate에 Deposition되는 방식입니다.
– CVD(Chemical Vapor Deposition)
CVD란 기체 상태의 화학적 성분들이 기판 위에서 화학 반응에 의해 박막을 형성하는 공정을 의미합니다. CVD 특징을 살펴보면 다음과 같습니다. Thin Film의 두께를 조절할 수 있고 Step Coverage 가 좋고 PVD 대비 공정비용이 낮아서 대량 생산이 가능하다는 장점이 있습니다. 또한 여러 종류의 원소 및 화합물을 증착 할 수 있으며 융점이 높아 제조하기 어려운 재료도 화학반응을 통해 융점보다 낮은 온도에서 용이하게 제조가 가능합니다 .
CVD Basic Process를 위 사진을 통해 정리하도록 하겠습니다. 반응기체가 확산에 의해 전달되어( Diffusion ) 표면에 흡착되고( Absorption ) 그에 따라 표면 반응이 일어나고 이동하게 됩니다( Surface reaction & migration ). 이 과정을 통해 생성된 부산물은 탈착되어( Desorption ) 제거됩니다. CVD는 열에 의한 것과 플라즈마에 의한 것으로 나눌 수 있습니다. 지금부터 자세히 CVD 세부공정에 대해 정리하도록 하겠습니다.
1. APCVD(Atmospheric Pressure CVD)
APCVD는 초기 CVD 공정방식으로 대기압 상태 에서 Deposition을 진행했습니다. CVD에서는 Pressure가 클수록 Throughput이 좋고 간단한 반응기 구조인 장점이 있습니다. 하지만 진공도가 낮아서 가스 분자 간 충돌이 많고 그로인해 Step Coverage 특성이 나빠서 현재는 사용하지 않는 방식입니다.
2. LPCVD(Low Pressure CVD)
Pressure를 APCVD보다 1/100 가량 낮춘 방식이 LPCVD로 이전 방식 대비 Step Coverage 가 우수하다는 장점이 있습니다. Pressure가 1/100 가량 낮아진 문제점은 온도를 APCVD 보다 2배 높게 하여 Throughput 문제를 보완했습니다. 하지만 1000도에 달하는 온도는 집적도가 높아진 트랜지스터 상부에 위치한 IMD와 같은 층 밑에 있는 메탈라인을 녹일 만큼 높은 온도입니다 . 그래서 저온 고진공 상태에서 우수한 Step Coverage를 가지며 Throughput이 좋은 CVD 방식을 개발해야했습니다. 바로 플라즈마 에너지를 이용한 PECVD입니다.
3. PECVD(Plasma Enhanced CVD)
PECVD는 다음과 같은 방식으로 진행합니다. 반응기체를 Chamber안에 주입하고 플라즈마 상태로 바꾸기 위해 높은 전압을 수직으로 걸어줍니다. 플라즈마 상태로 이온화된 기체들은 서로 화학반응을 하여 원하는 물질은 Deposition되고 나머지는 결합하여 Chamber 밖으로 빠져나가는 방식입니다. PECVD의 장점은 저온공정 임에도 불구하고 Throughput이 좋습니다 . 하지만 Step Coverage 문제가 발생한다는 단점이 있습니다.
4. HDPCVD(High Density Plasma CVD)
PECVD의 Step Coverage 를 개선한 방식이 바로 HDPCVD입니다. 따라서 최신 공정에서는 HDPCVD를 주로 사용하고 있고 PECVD는 Thin Film의 질이 상대적으로 낮아도 괜찮은 부분에만 국부적으로 사용하고 있습니다. HDPCVD의 원리는 고밀도의 플라즈마를 통해 Etching과 Deposition 을 번갈아서 반복 하므로 Void와 같은 Defect 발생확률을 낮춥니다 .
5. ALCVD(Atomic Layer CVD)
마지막으로 ALCVD에 대해 정리하겠습니다. ALD라고도 불리는데요, PVD와 CVD보다 advanced한 공정이라고 할 수 있습니다. 그 이유는 저온공정 으로 더욱 얇은 막을 형성할 수 있고 Step Coverage와 Uniformity가 가장 좋습니다 . ALD의 유일한 단점인 Throughput 문제를 개선하기 위해 플라즈마를 이용한 PEALD 방식을 활용하는 추세입니다. 위 사진은 Al2O3를 Deposition하는 과정입니다. 공정 Step은 4단계로 분류할 수 있습니다. 표면흡착, 치환, 신규막 생성, 가스배출 순으로 공정이 이루어집니다.
<출처 : ALD Atomic Layer Deposition - Thin Films and Nanotechnology by Warsash Scientific>
반도체 공정 – 박막 공정(PVD)
728×90
SMALL
박막 공정
#시작하며
지난 포스팅까지는 반도체 8대 공정 중, 포토 공정을 거치고 정의된 박막의 일부 또는 전부를 물리, 화학적으로 제거하는 식각 공정을 공부하였다. 이번에는 2번에 걸쳐 이후 과정인 박막 증착 공정에 대해 알아볼 것이다. 박막 증착 공정은, 여러층을 쌓아 바로 아래층의 회로가 위층의 회로와 가까워지면, 서로에게 영향을 주기 때문에 불량 제품이 생산될 수 있기 때문에, 아래층과 위층의 회로가 서로 영향을 주지 않도록 얇은 절연막을 덮어주는 역할을 한다.
#박막 공정
박막 증착 공정을 공부하기에 앞서, 박막은 무엇이고 또 증착은 무엇일까?
박막(Thin Film)이란, 기계가공으로는 실현 불가능한 두께인 1μm 이하의 얇은 막을 지칭한다. 다음으로 증착(Deposition)은, 전기적 특성이 없는 웨이퍼 위에, 원하는 분자 또는 원자 단위의 물질을 박막의 두께로 입혀 전기적 특성을 갖게 하는 일련의 과정을 의미한다.
이러한 증착(Deposition)은, 크게 두가지로 분류할 수 있는데, 물리기상증착법인 PVD(Physical Vapor Deposition)와 화학기상증착법인 CVD(Chemical Vapor Deposition) 가 있다.
증착의 필요 스펙
1. Quality : 전기적/물리적 특성의 품질
2. Thickness Uniformity : 웨이퍼의 균일도와 웨이퍼 간의 균일도 등
3. Step Coverage: 증착 후 바닥부분 박막의 두께와 탑 부분의 기판에 쌓여있는 비율이 일정한지에 대한 여부
출처. 한국기술교육대학교
Step Coverage는, 위 그림의 s와 t의 비율인 s/t이며, 균일화가 얼마나 잘 이루었는지를 의미하기 때문에, 1에 가까울수록 좋은 Step Coverage가 나타난다고 할 수 있다. 하지만 실제로 공정을 진행해보면, 탑 부분은 정상적으로 증착이 되지만, 측벽 부분은 균일하지 않게 탑 부분보다 얇게 증착이 되는 것을 알 수 있다. 이외에도 Aspect Ratio(종횡비)는 h/w이며, 균일화의 어려움 척도를 나타내는 수치이다.
(a). Good, (b) Poor, Step Coverage
4. Filling : Filling은 말그대로 단차 사이 공간을, 빈 공간 없이 잘 채우는지에 대한 여부를 의미한다.
위 그림에서 단계별 증착 과정에서, 단차 사이에 빈 공간 Void가 생겨 결함이 발생한다.
PVD(Physical Vapor Deposition)
PVD는 물리적기상증착으로서, 금속 증착에 주로 사용하고, 낮은 압력과 낮은 온도에서 진행된다. 따라서 고품질의 방막을 형성하고 불순물 오염 정도가 낮다는 장점이 있지만, 증착 속도가 드리고 고가의 장비를 사용해야 한다는 단점이 있다.
* Thermal Evaporation
출처. http://www.semicore.com/images/photos/thermal-evaporation-process.png
Themal Evaporation은, 증착시키고자 하는 물질을 보트에 올려두고 가열함으로써 증착 물질을 증발시켜 기판에 증착하는 방식이다. 고진공 Chamber에서 가열이 진행되며, 물질이 등방성의 성질로 퍼지기 때문에 낮은 Step Coverage를 가진다.
* E-beam Evaporation
출처. http://www.semicore.com/images/photos/diagram-ebeam-evaporation.png
E-beam은, Thermal Evaporation과 동일한 방식으로 진행되지만, Deposition하고자 하는 물질에 열 대신 E-beam을 가해 증발을 시킨다는 차이가 있다. 낮은 Step Coverage를 가지는 Thermal Evaporation을 보완하여, 높은 에너지의 E-beam을 통해 플라즈마 상태로 만든 후 DC 전압을 인가하는 방식으로 진행하여 개선한다.
* Sputttering
출처. http://www.semicore.com/images/photos/diagram-sputtering-process.png
Sputtering은 증착시키려는 물질의 Target을 Chamber 상단에 두고, 이온을 이용하여 Target 물질을 웨이퍼에 증착시키는 방식이다. Vaccum state에서 기판은 (+), Target은 (-) 전하를 걸어주고 비활성 Ar 가스를 주입한다. 그 후 전압을 인가하면 (+)로 가속하는 전자와 Ar원자가 충돌하며 이온이 발생하고, 홰당 이온은 Target의 (-)으로 이동하여 충돌하는 과정을 통해 Target의 원자들이 방출되어 (+)인 기판에 증착된다.
#마치며
이번 포스팅에는, 박막 증착 방법 중 하나인 PVD(Physical Vapor Deposition), 물리기상증착법에 대해 알아보았다. 다음에는 다른 한 가지 방법인 CVD에 대해 논의하며 공부해볼 것이다.
728×90
키워드에 대한 정보 박막 증착 공정
다음은 Bing에서 박막 증착 공정 주제에 대한 검색 결과입니다. 필요한 경우 더 읽을 수 있습니다.
이 기사는 인터넷의 다양한 출처에서 편집되었습니다. 이 기사가 유용했기를 바랍니다. 이 기사가 유용하다고 생각되면 공유하십시오. 매우 감사합니다!
사람들이 주제에 대해 자주 검색하는 키워드 원숭이가 이해하기에는 조금 어려운 증착공정, 이온주입, CVD, PECVD, ALD, AMAT, 유진테크, 원익IPS, 주성엔지니어링
- 증착공정
- 반도체증착
- 이온주입
- 이온주입공정
- ALD
- CVD
- PECVD
- PEALD
- AMAT
- 유진테크
- 원익IPS
- 주성엔지니어링
원숭이가 #이해하기에는 #조금 #어려운 #증착공정, #이온주입, #CVD, #PECVD, #ALD, #AMAT, #유진테크, #원익IPS, #주성엔지니어링
YouTube에서 박막 증착 공정 주제의 다른 동영상 보기
주제에 대한 기사를 시청해 주셔서 감사합니다 원숭이가 이해하기에는 조금 어려운 증착공정, 이온주입, CVD, PECVD, ALD, AMAT, 유진테크, 원익IPS, 주성엔지니어링 | 박막 증착 공정, 이 기사가 유용하다고 생각되면 공유하십시오, 매우 감사합니다.